Trusted by 2.000+ leading companies in the Food Service & Retail and Healthcare & Pharma industry
We serve over 2.000+ companies in several industries. Read their success stories.
Discover what Rmoni can do for your industry
Up to 40% lower cost of quality with Rmoni's solution
Implementing Rmoni’s revolutionary Digital Quality Management Solution in 3 simple steps
Our implementation experts know what you need. Here's how they will help you set up.
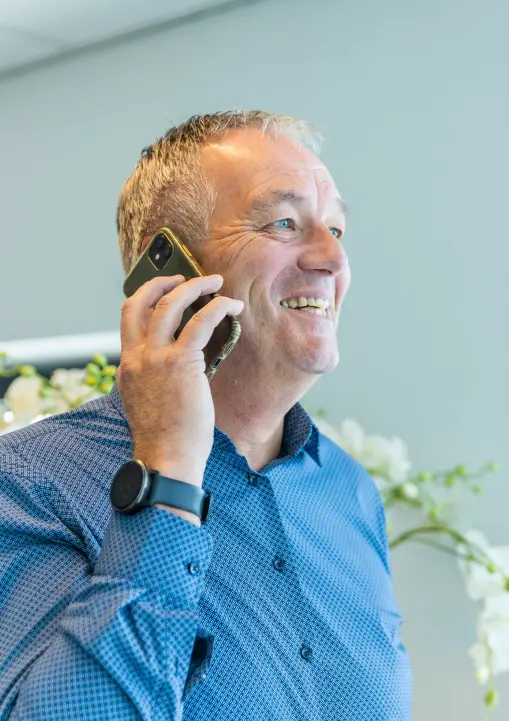
Meet the most recent regulations and requirements
Whether in Food Service & Retail or Healthcare & Pharma, Rmoni helps you attain full compliance in any sector.
Van Der Valk: Moving from manual registration to digital convenience
Stop drowning in senseless paperwork
Say goodbye to paper, pen and manual checklists and start automating your Digital Quality Management
We're here for all your
quality related questions
Digital quality management (DQM) is the digitized process of ensuring that products & processes meet quality standards and are fit for purpose. It involves digitally measuring and monitoring performance against set quality standards standards, and taking corrective actions when necessary.
A quality management system (QMS) is a collection of business processes and resources that are used to manage quality throughout an organization. The QMS is designed to help organizations meet their customers' needs and expectations while also meeting regulatory requirements.
An effective QMS provides a framework for quality planning, assurance, and control. It is used to manage and improve an organization’s quality policies, objectives, and responsibilities. A QMS can be used to assess and improve an organization’s quality performance.
It can also be used to monitor compliance with, for instance, ISO quality system requirements. For heavily-regulated businesses operating in the food industry, healthcare, or cold chain logistics, QMS is especially critical to staying in business.
HACCP, or Hazard Analysis and Critical Control Points, is a systemic approach for managing food safety.
It is used to prevent biological, chemical, and physical hazards from entering into food production processes, in order to prevent the finished product from being unsafe for consumption.
Beyond it being mandatory to have an HACCP-plan within restaurants, cafés, or food manufacturing plants, pharmaceutical and cosmetic companies are also increasingly adopting this system.
In order to successfully implement HACCP and make executing the necessary procedures feasible, digital HACCP registration is preferred over paper documents.
Lists of all ingredients, final products and their intermediary production processes, for example, can easily be stored online for all members of the HACCP-team to access and share.
And beyond all the documentation, a digital HACCP solution allows for real-time monitoring and alarming regarding CCPs, by connecting to measuring equipment like temperature monitoring sensors and air quality sensors.